The Rise of CNC Parts Factories: Leading the Future of Manufacturing
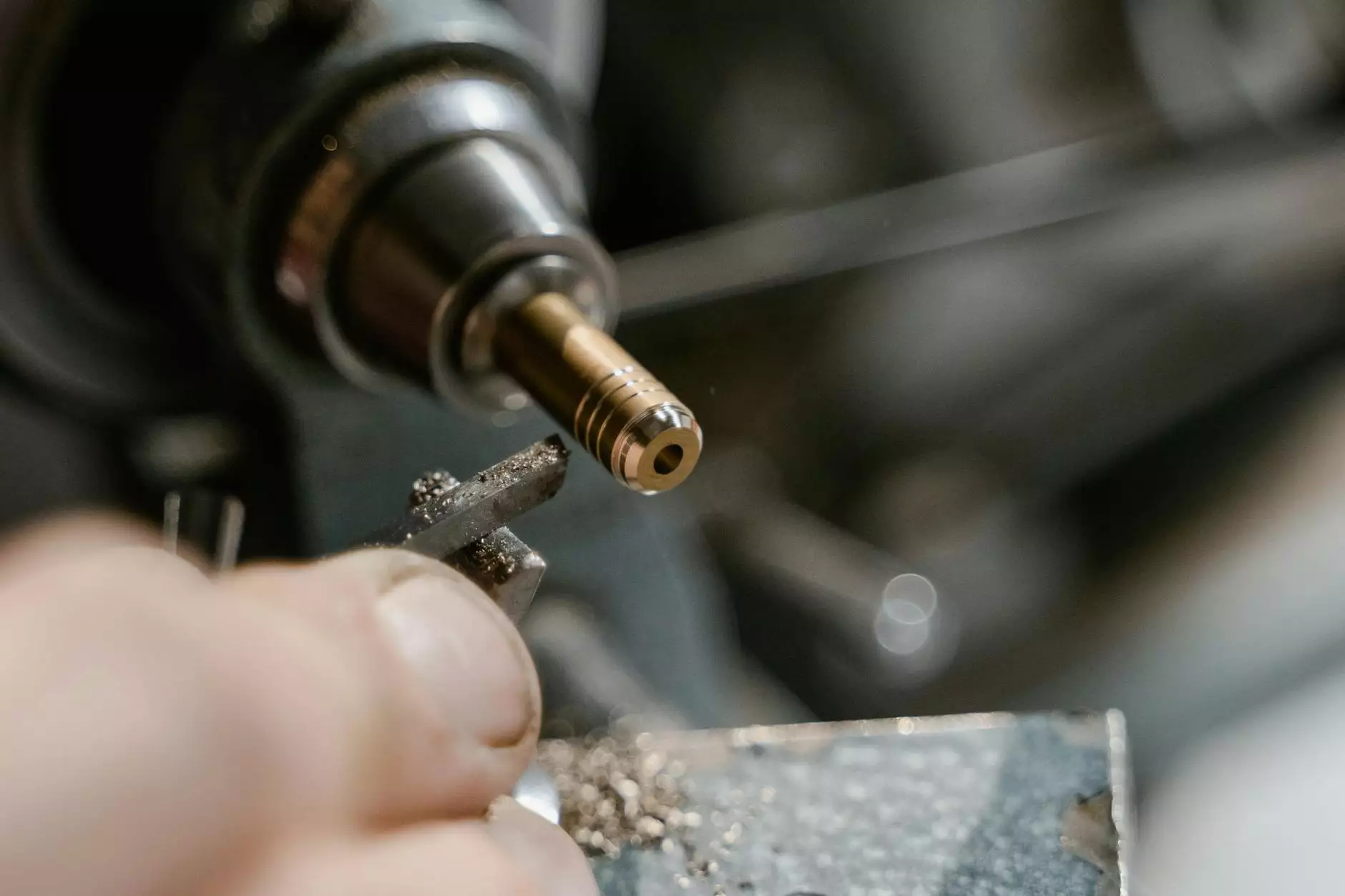
In the ever-evolving landscape of manufacturing, CNC parts factories are becoming synonymous with precision, efficiency, and innovation. As businesses strive to enhance productivity while minimizing costs, CNC (Computer Numerical Control) technology has established itself as a game changer in the metal fabrication industry. This article delves into the pivotal role of CNC parts factories, examining their benefits, technologies, and impact on the modern manufacturing sector.
Understanding CNC Technology
CNC technology represents a significant advancement over traditional machining processes. Unlike manual machines, CNC machines operate through computer programming, allowing for intricate, precise designs that are often unattainable through manual operations. The core components of CNC technology include:
- CNC Machines: These machines are equipped with motors and computers that execute precise movements.
- Computer Software: Advanced software programs allow designers to create and simulate intricate parts before production.
- Materials: From metals to plastics, CNC parts factories can work with a variety of materials, enhancing versatility.
The Advantages of CNC Parts Factories
The benefits of utilizing a CNC parts factory are extensive, making them an attractive option for businesses in need of high-quality manufacturing. Here are the primary advantages:
- Precision and Consistency: CNC machines can produce parts with astonishing accuracy, maintaining tight tolerances that are critical in industries like aerospace and automotive.
- Efficiency: The automation of CNC machining significantly speeds up the manufacturing process, allowing businesses to meet tight deadlines without sacrificing quality.
- Cost-Effectiveness: While the initial investment in CNC technology may be higher than traditional methods, the reduction in waste and labor costs leads to improved profitability over time.
- Versatility: CNC machines can be programmed to produce a wide range of components, making them ideal for various sectors, from medical devices to electronics.
- Reduced Human Error: As processes are automated, the risk of human error is minimized, leading to fewer defects and a better end product.
How CNC Parts Factories Work
Understanding the workflow of a CNC parts factory can help businesses appreciate how products are brought to life. The process generally follows these stages:
1. Design and Prototyping
The journey begins with design, where engineers and designers create the specifications of the part using CAD (Computer-Aided Design) software. This digital blueprint serves as the foundation for the CNC machining process. Prototyping can also take place during this phase to verify design effectiveness.
2. Programming the CNC Machine
Once the design is finalized, it is translated into a language that CNC machines can understand, known as G-code. This code instructs the machine on how to move, cut, and shape the material.
3. Production
The CNC machine executes the programmed commands to manufacture the part. This stage involves loading raw materials, setting machine parameters, and monitoring the production process for quality assurance.
4. Post-Processing and Finishing
After the initial machining, components may require additional processing, such as polishing, coating, or assembly. This ensures that the final product meets the required specifications and performance standards.
Key Technologies in CNC Parts Factories
The advancement of technology continues to enhance the capabilities of CNC parts factories. Some of the key technological innovations include:
1. Additive Manufacturing Integration
Combining traditional CNC machining with additive manufacturing allows for the creation of complex geometries and lightweight structures, granting engineers greater freedom in design.
2. IoT and Smart Factories
The Internet of Things (IoT) brings intelligence to CNC manufacturing by connecting machines and systems, enabling real-time data analysis, predictive maintenance, and enhanced operational efficiency.
3. Virtual Reality (VR) and Augmented Reality (AR)
VR and AR technologies facilitate training and design verification, providing immersive experiences that help engineers and operators visualize complex processes before execution.
Choosing the Right CNC Parts Factory
Selecting the appropriate CNC parts factory is critical for business success. Here are some essential factors to consider:
1. Capability and Capacity
Ensure the factory has the necessary capabilities to produce your specific parts with the desired materials, tolerances, and finishes. Additionally, assess whether the factory can handle your order volume and deadlines.
2. Quality Assurance
Look for factories that employ rigorous quality control processes. Certifications such as ISO 9001 or AS9100 can be indicators of high standards in production and quality management.
3. Technological Advancements
Evaluate the technology employed by the factory. The latest CNC machinery and software can drastically improve production efficiency and part quality.
4. Customer Service and Communication
Choose a CNC parts factory that values customer service and maintains open lines of communication throughout the production process. This ensures transparency and allows for adjustments as needed.
Future Trends in CNC Parts Factories
As industries evolve, CNC parts factories will continue to adapt. Significant trends expected to shape the future of CNC manufacturing include:
1. Sustainable Practices
Increasing emphasis on sustainability will lead CNC parts factories to adopt eco-friendly practices, focusing on reducing waste and utilizing renewable materials.
2. Customization and Personalization
The demand for customized products is on the rise, and CNC technology will enable factories to efficiently produce one-off parts without sacrificing quality or speed.
3. Continued Automation
Further advancements in automation will streamline production processes, reduce labor costs, and allow for 24/7 operation, making CNC parts factories more competitive.
4. Enhanced Collaboration with AI
The integration of AI in CNC systems will facilitate smarter manufacturing, including predictive analytics for maintenance, optimized machining paths, and real-time quality monitoring.
Conclusion
In conclusion, CNC parts factories are indispensable to the modern manufacturing landscape. Their ability to deliver unparalleled precision, efficiency, and flexibility makes them a cornerstone of innovation across various industries. As technology continues to advance, these factories will only become more integral to meeting the demands of a rapidly changing market. Businesses looking to leverage CNC capabilities should consider partnering with a reputable CNC parts factory to capitalize on the numerous benefits offered by this advanced manufacturing process. Explore your options and embrace the future of manufacturing to drive your business success.
For more insights into CNC parts manufacturing, visit deepmould.net