Molding Plastic Injection: Revolutionizing the Manufacturing Landscape
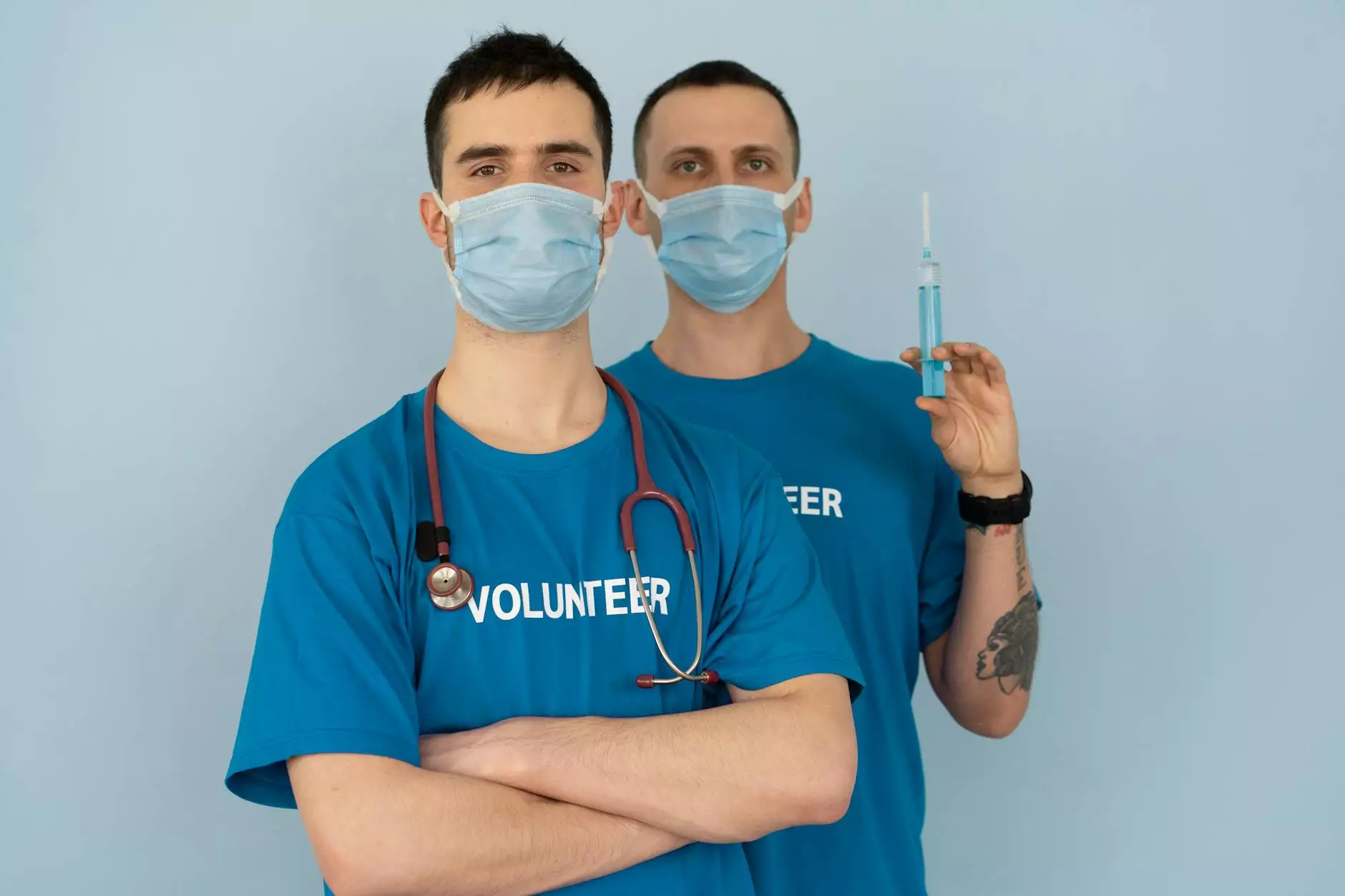
Molding plastic injection is a pivotal process within modern manufacturing, offering unparalleled efficiency and precision. This technique is crucial for manufacturers looking to produce complex parts with a high degree of accuracy while optimizing costs and reducing waste. In this extensive article, we will explore the intricacies of molding plastic injection, its applications across different industries, and the advantages it presents to businesses like Deep Mould in the category of Metal Fabricators.
Understanding Molding Plastic Injection
Molding plastic injection is a process by which plastic materials are heated until they melt, then injected into a mold where they cool and solidify to form a specific shape. This method is widely utilized in various sectors due to its versatility and efficiency.
The Process of Molding Plastic Injection
The molding plastic injection process can be broken down into several key steps:
- Material Preparation: The first step involves selecting the appropriate plastic resin, which is then dried to remove any moisture.
- Heating: The resin is heated in an injection unit until it reaches a molten state, allowing for easier injection into the mold.
- Injection: The molten resin is injected into the mold cavity under high pressure, ensuring that every detail is captured.
- Cooling: The mold is cooled to solidify the plastic, after which the mold is opened to release the finished part.
- Finishing: Any excess material is trimmed, and the product is inspected for quality before it is shipped.
Applications of Molding Plastic Injection
This innovative technique is employed across a vast spectrum of industries, playing a critical role in the production of components that are integral to daily life. Below are some notable applications:
1. Automotive Industry
The automotive sector greatly benefits from molding plastic injection. From dashboards to interior components, manufacturers use this method to create lightweight yet durable parts. This not only enhances performance but also improves fuel efficiency by reducing vehicle weight.
2. Consumer Goods
Many everyday items, such as kitchen utensils, toys, and electronic housings, are produced using molding plastic injection. The ability to produce intricate designs at scale allows manufacturers to meet consumer demands and maintain quality standards.
3. Medical Devices
The precision required in producing medical devices makes molding plastic injection indispensable in the healthcare industry. Components such as syringes, valves, and housings for sensitive equipment are often manufactured using this method, ensuring reliability and safety.
4. Packaging Industry
Packaging solutions, including containers and closures, often utilize molding plastic injection. The versatility of the materials allows for adaptations to meet strict regulatory requirements, especially in food and pharmaceuticals.
5. Electronics
Molding plastic injection is crucial in the electronics industry for creating housings and connectors. It facilitates the production of complex designs that can accommodate intricate circuitry and components.
Advantages of Molding Plastic Injection
Businesses that adopt molding plastic injection can reap numerous advantages, which contribute to enhanced productivity and profitability:
1. Cost Efficiency
One of the most significant benefits of molding plastic injection is its cost-efficiency. Once the initial mold is created, the cost per part decreases substantially with higher production volumes. This makes the method particularly attractive for high-volume outputs.
2. High Quality and Precision
Molding plastic injection offers exceptional accuracy, which is essential in manufacturing quality products. The process allows for tight tolerances, ensuring that parts fit together perfectly, which is critical in applications where precision is paramount.
3. Versatility of Materials
Manufacturers can choose from a wide variety of materials, including various grades of plastic that offer different qualities such as strength, flexibility, and durability. This versatility allows businesses to select the most suitable material for their needs.
4. Reduced Waste
Unlike traditional manufacturing methods, molding plastic injection produces minimal waste. The process allows for excess material to be reheated and reused, further enhancing cost savings and sustainability.
5. Automation and Scalability
Molding plastic injection can easily be integrated into automated production lines. This facilitates scalability, allowing businesses to adjust production rates in response to market demands without compromising quality.
Innovations in Molding Plastic Injection
As industries evolve, so too does technology in molding plastic injection. Innovations are constantly being introduced to enhance efficiency and capabilities:
1. Advanced Materials
Research and development are leading to the creation of advanced polymer materials that can withstand extreme conditions or possess enhanced properties, like biocompatibility for medical applications.
2. 3D Printing Integration
The integration of 3D printing technology with molding plastic injection is enabling rapid prototyping and faster production cycles. This allows businesses to test designs quickly and optimize molds prior to large-scale production.
3. Smart Manufacturing Technologies
The adoption of IoT and AI within the molding plastic injection process is paving the way for smarter manufacturing environments. These technologies enable real-time monitoring and adjustments, enhancing efficiency and reducing downtime.
Challenges Facing the Industry
Despite its advantages, the molding plastic injection industry does face challenges, including:
1. Initial Setup Costs
The initial investment in molds and machinery can be substantial. For small businesses, this can be a barrier to entry, necessitating careful budgeting and planning.
2. Technological Skills Gap
The rapid advancement of technology requires workforce training and development to keep up with new techniques and equipment. Closing this skills gap is crucial for maintaining competitive advantage.
3. Environmental Concerns
With the growing focus on sustainability, the plastic waste generated in the molding plastic injection process is under scrutiny. Manufacturers must develop more sustainable practices and consider alternatives to traditional materials.
Conclusion: The Bright Future of Molding Plastic Injection
In conclusion, molding plastic injection is more than just a manufacturing process; it is a transformative force in the Metal Fabricators industry and beyond. Its numerous applications, coupled with its capacity for innovation and adaptation, make it an essential method for businesses looking to thrive in a competitive landscape. By embracing the advantages of molding plastic injection, manufacturers can not only increase efficiency and reduce costs but also improve the quality of their products, satisfying the ever-evolving demands of consumers.
For manufacturers wishing to leverage the full potential of molding plastic injection, partnering with experienced providers like Deep Mould can offer invaluable insights and support, ensuring success in this exciting manufacturing landscape.