CNC Machining Lathe Machine Parts: A Comprehensive Guide
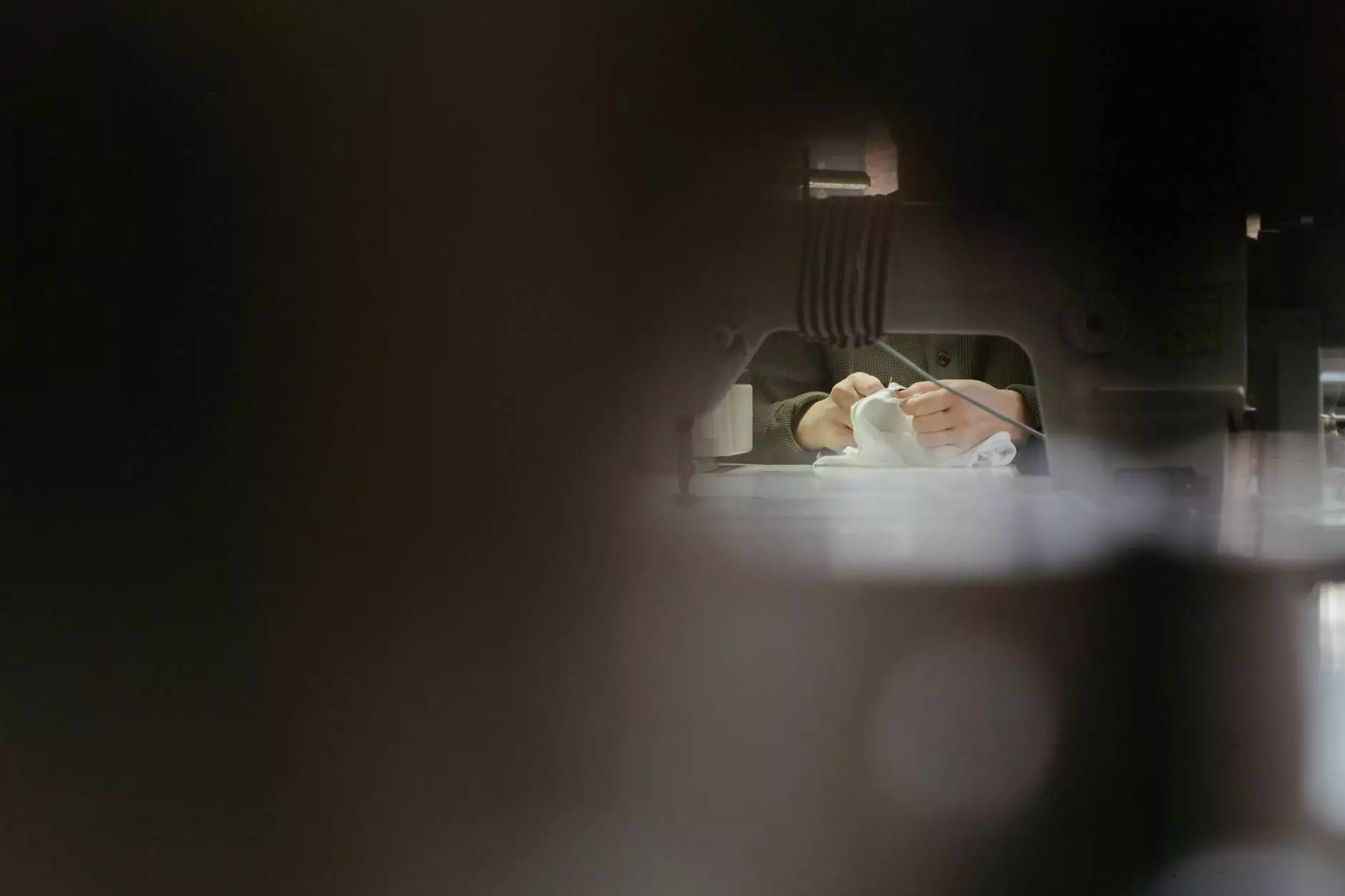
In the realm of modern manufacturing, CNC machining has emerged as a pivotal technology, particularly when it comes to the fabrication of lathe machine parts. This article delves deep into the world of cnc machining lathe machine parts, exploring their importance, the technologies behind them, and the various applications across industries.
Understanding CNC Machining
CNC stands for Computer Numerical Control. It refers to the automation of machine tools via computers executing pre-programmed sequences of machine control commands. CNC machining is a key process in modern manufacturing, allowing for precise and repeatable production of components with complex geometries.
How CNC Machining Works
The process begins with a digital design file, often created in CAD (Computer-Aided Design) software. The CAD file is converted into a format that the CNC machine can understand, typically through CAM (Computer-Aided Manufacturing) software. This set of instructions guides the machine in cutting, drilling, milling, or turning materials to produce the desired parts.
The Role of Lathe Machines in Manufacturing
A lathe machine is a critical tool in the manufacturing process, known for its ability to rotate a workpiece against a cutting tool. This rotational motion allows for the creation of symmetrical parts and intricate designs. CNC lathe machines have revolutionized this process through automation, leading to improved efficiency and accuracy.
Types of CNC Lathe Machines
- Horizontal CNC Lathes: These are the most common types, ideal for a wide range of applications.
- Vertical CNC Lathes: Used for larger workpieces, these machines are designed for greater stability.
- Multi-Spindle Lathes: These lathes can operate multiple spindles simultaneously, significantly increasing productivity.
Components of CNC Lathe Machines
Understanding the components involved in CNC lathe operations is essential for comprehending the intricacies of cnc machining lathe machine parts.
Main Components
- Headstock: Houses the main motor that drives the spindle and provides the mechanisms for tool changes.
- Tailstock: Provides support for the workpiece, especially for longer items.
- Bed: The foundation of the lathe machine, supporting all other components.
- Carriage: Contains the mechanism that moves the cutting tool and can be adjusted for various operations.
- Control System: The CNC interface that allows operators to input parameters and control the machining process.
Benefits of CNC Machining Lathe Machine Parts
The adoption of CNC machining for lathe machine parts brings forth a plethora of advantages:
Precision and Accuracy
One of the most significant benefits is the high degree of precision and accuracy that can be achieved. CNC machines can reproduce parts to tolerances of ±0.001 inches, ensuring that every part fits perfectly in its designated application.
Complex Part Production
With CNC lathe machines, manufacturers can produce complex geometries that were previously impossible or too costly to achieve with traditional manual methods.
Efficiency and Speed
Automation leads to reduced cycle times and increased throughput, allowing manufacturers to meet high-volume demands without compromising quality.
Applications of CNC Machining Lathe Machine Parts
The versatility of CNC machining positions it for a wide range of applications across numerous industries. Here are some key sectors utilizing this technology:
Aerospace Industry
In aerospace, precision is paramount, and CNC machined parts are vital for components like brackets, gears, and housings that must withstand extreme conditions.
Automotive Industry
The automotive sector leverages CNC machining for producing engine components, transmission parts, and custom pieces for performance vehicles.
Medical Devices
In the realm of medical device manufacturing, CNC machining ensures that the intricate parts of devices such as surgical instruments and prosthetics are produced to exacting standards.
Choosing the Right CNC Machining Service
When seeking to acquire cnc machining lathe machine parts, it is vital to select a reputable service provider. Here are some factors to consider:
Expertise and Experience
Look for a company with a proven track record in CNC machining. Their experience will equip them to handle complex projects and deliver high-quality results.
Technology and Equipment
Ensure that the provider utilizes the latest CNC technology and machines to maintain accuracy and efficiency. Advanced toolpaths and programming can significantly affect outcomes.
Quality Assurance Processes
A company should have stringent quality control measures in place. This includes regular inspections, adherence to industry standards, and certifications that validate their processes.
Future Trends in CNC Machining
The world of CNC machining is ever-evolving, with constant advancements shaping its future. Here are a few trends to watch:
Integration of Artificial Intelligence
AI is increasingly being integrated into CNC machining operations to enhance predictive maintenance, optimize production processes, and reduce downtime.
Increased Automation
As manufacturers look to improve efficiency, the use of advanced robotics alongside CNC machines is becoming more commonplace, facilitating a more streamlined production environment.
3D Printing and Hybrid Methods
The fusion of CNC machining with 3D printing technology is paving the way for hybrid manufacturing processes, allowing for greater design flexibility and material efficiency.
Conclusion
As industries continue to evolve, the importance of cnc machining lathe machine parts cannot be overstated. Their role in producing high-quality, precise components will only increase with technological advancements and the drive for greater efficiency in manufacturing processes. At DeepMould.net, we are committed to providing our clients with the highest quality CNC machining services to meet their diverse needs.
The world of CNC machining is expanding rapidly, and understanding the intricacies of the processes involved will equip businesses to make informed decisions. Embrace this technology to elevate your manufacturing capabilities and stay ahead in today's competitive landscape.