Understanding the Role of a Plastic Parts Mould Manufacturer
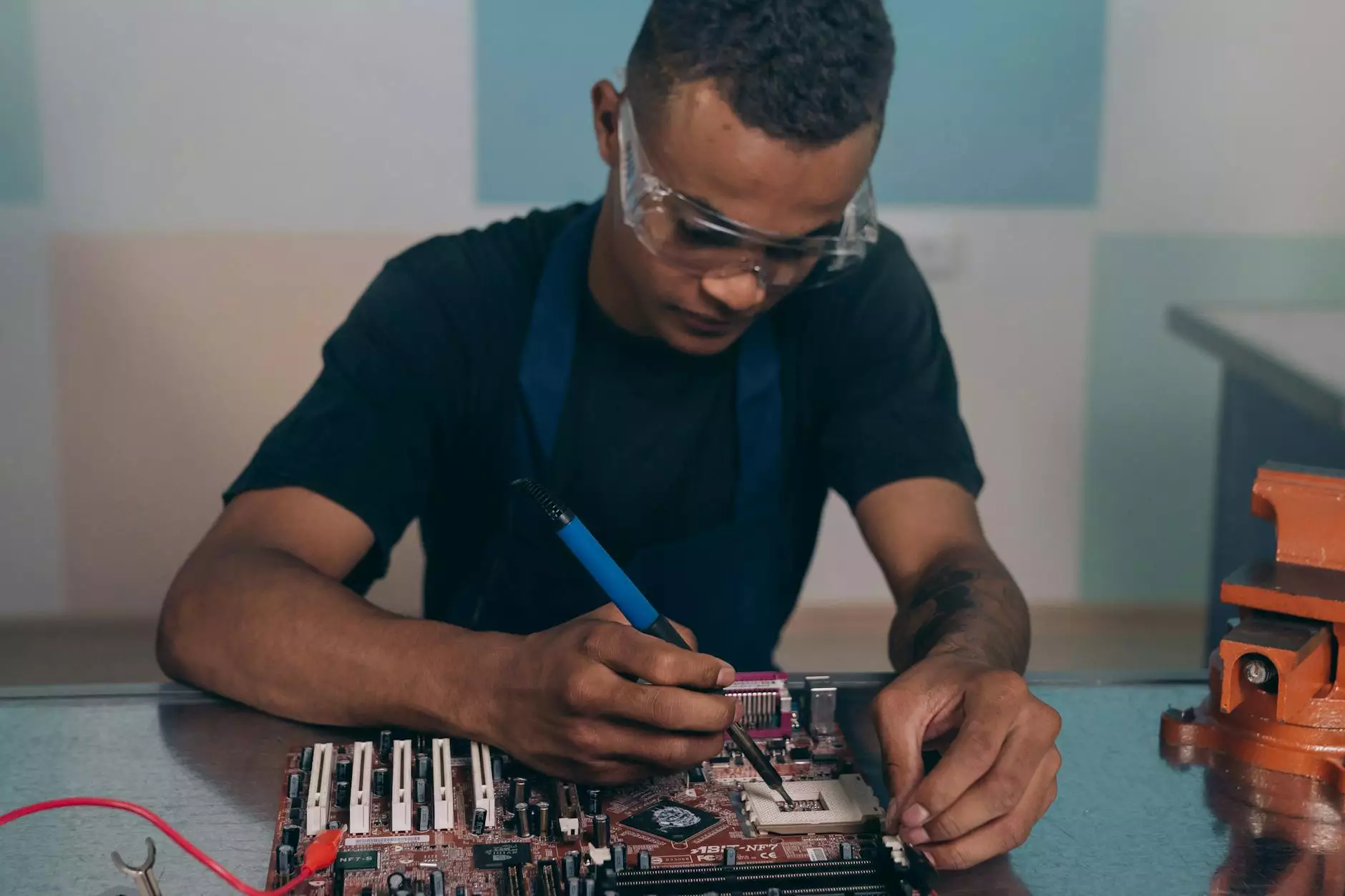
In today's rapidly evolving industrial landscape, the demand for precision and efficiency is more pronounced than ever. When it comes to manufacturing, plastic parts have become integral in various sectors, ranging from automotive to consumer electronics. At the heart of this process lies the expertise of a plastic parts mould manufacturer, a key player in bringing innovative concepts to life through effective moulding processes.
What is a Plastic Parts Mould Manufacturer?
A plastic parts mould manufacturer specializes in the production of molds that are used to create various plastic components. These molds are designed meticulously to ensure that the final products meet the desired specifications and quality standards. Manufacturers like Hanking Mould provide a variety of services, including:
- Design and Development: Crafting tailored solutions to meet specific customer needs.
- Prototype Creation: Building prototypes for testing and validation before mass production.
- Mass Production: Utilizing advanced injection moulding techniques for high-volume output.
- Quality Assurance: Ensuring every product adheres to strict quality control measures.
Why Choose a Professional Plastic Injection Mould Manufacturer?
When selecting a plastic injection mould manufacturer, several factors merit consideration. Here are the top reasons why working with a professional manufacturer, such as Hanking Mould, can be beneficial:
- Expertise and Experience: Established manufacturers possess extensive industry knowledge, ensuring they can handle diverse projects efficiently.
- Advanced Technology: Access to cutting-edge machinery and software enhances precision and reduces lead times.
- Customization: Ability to produce custom molds that cater to unique specifications.
- Cost-Effectiveness: Efficient production processes can significantly reduce material waste and lower costs in the long run.
- Reliability: A reputable manufacturer guarantees timely delivery and excellent customer service.
The Moulding Process Explained
The process of creating plastic parts involves several stages, each vital to the final outcome. Here’s a closer look at the production process used by leading plastic parts mould manufacturers:
1. Concept Development
Every project begins with a concept. Manufacturers collaborate closely with clients to understand their needs and provide input on design feasibility and functionality.
2. Mold Design
Once the concept is solidified, engineers use Computer-Aided Design (CAD) software to create detailed mould designs. This stage is critical, as it incorporates all specifications required for the final product.
3. Prototyping
Before moving forward with mass production, manufacturers create prototypes. This practice aids in identifying potential issues in design or functionality, ensuring that changes can be made without incurring significant costs.
4. Mould Fabrication
The actual mould fabrication follows successful prototyping. This phase involves intricate machining and shaping of materials like steel or aluminum, depending on the desired longevity and cost-effectiveness of the mould.
5. Injection Moulding
During this crucial stage, raw plastic is heated until it becomes pliable and is then injected into the mould. After cooling, the mould is opened to reveal the newly formed plastic part.
6. Quality Control
Quality assurance checks are imperative. Every batch of produced parts undergoes rigorous examination to ensure they meet the established quality standards.
Advantages of Using Plastic Parts in Manufacturing
Plastic remains a preferred material in manufacturing due to its versatility and numerous benefits. Here are some advantages of using plastic parts:
- Lightweight: Plastic components are significantly lighter than metal counterparts, making them ideal for applications requiring reduced weight.
- Corrosion Resistance: Plastic is not susceptible to rust or corrosion, enhancing the durability of products.
- Design Flexibility: The ease of molding allows for complex shapes and designs that would be difficult or costly with other materials.
- Cost-Effectiveness: Generally, plastic parts are more cost-efficient than those made from metal, particularly in high-volume productions.
- Insulation Properties: Many plastics are excellent insulators, making them suitable for electrical applications.
Choosing the Right Plastic Parts Mould Manufacturer
Choosing the right plastic parts mould manufacturer is a crucial part of ensuring your project’s success. Here are several factors to consider:
1. Portfolio and Experience
Examine the manufacturer’s previous work to gauge their capabilities and the industries they have experience with. A diverse portfolio can be a good indicator of versatility.
2. Technology and Equipment
Investigate whether the manufacturer uses modern and well-maintained machinery. Advanced technology can lead to lower production costs and higher quality output.
3. Customer Support
Look for manufacturers that provide excellent customer service. This includes support during the design phase, quick responses to inquiries, and assistance throughout the manufacturing process.
4. Lead Times
Discuss expectations regarding lead times. A reliable manufacturer can provide clear timelines and meet deadlines consistently.
5. After-Sales Service
Consider manufacturers that offer robust after-sales support, including feedback and adjustments if necessary. This commitment to customer satisfaction can greatly enhance the overall experience.
Conclusion
In conclusion, selecting the right plastic parts mould manufacturer is imperative for any business looking to innovate and streamline production. Manufacturers like Hanking Mould exemplify what it means to provide high-quality, reliable services that cater to modern manufacturing needs. With their expert knowledge and advanced technology, they ensure that every plastic part is produced to the highest standards, supporting businesses in achieving their objectives efficiently and effectively.
By understanding the intricacies of the moulding process and the significant advantages of employing expert manufacturers, companies can better navigate the complexities of modern production. Investing in the right partnerships today will undoubtedly pave the way for greater innovation and growth in the future.