Understanding the Importance of Die Casting Mold in Metal Fabrication
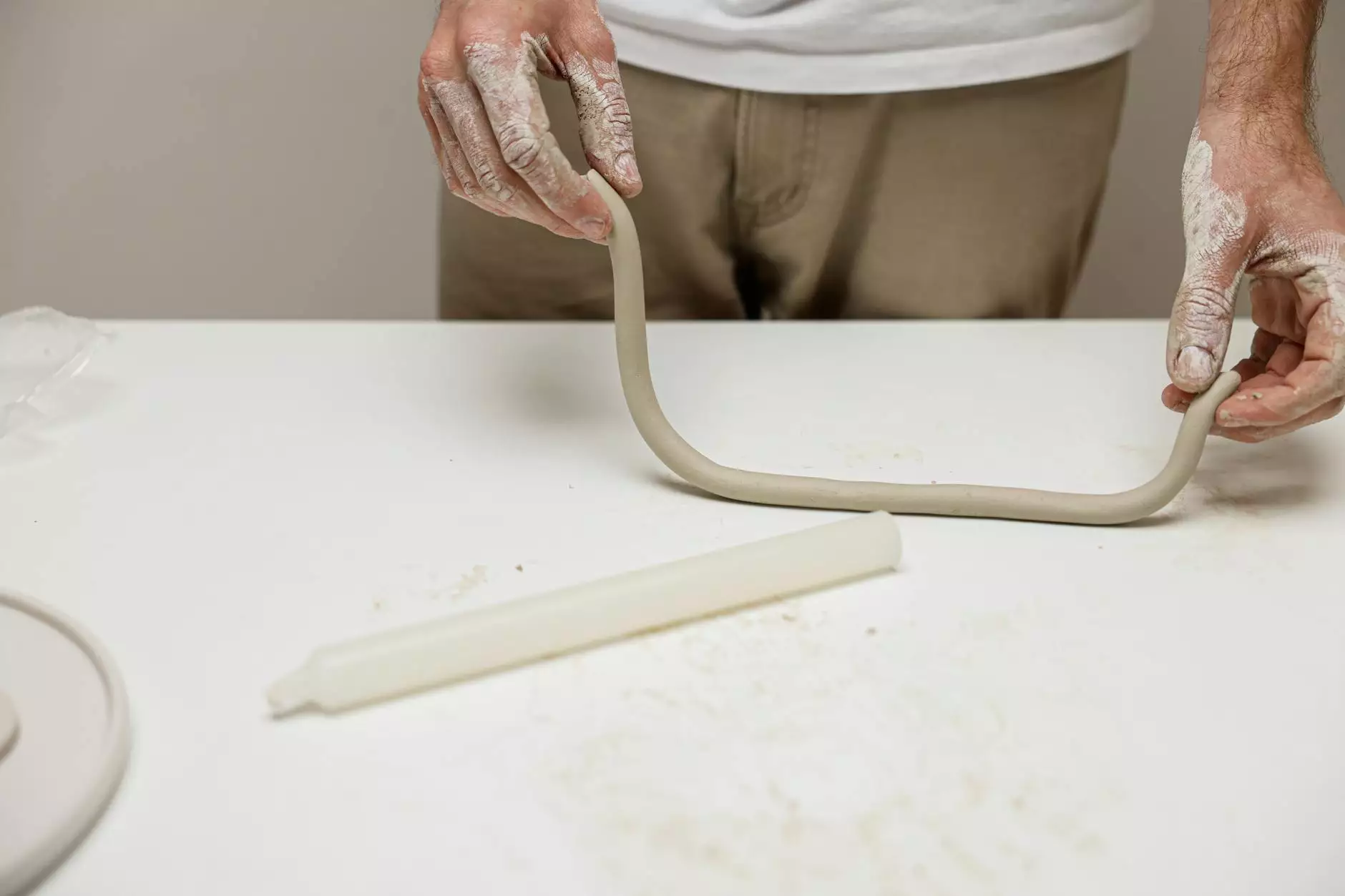
In the world of manufacturing, few processes are as crucial as metal fabrication. Among the various techniques employed, die casting stands out due to its efficiency and ability to produce complex shapes with high precision. At the heart of this process lies the die casting mold, a vital component that dictates the quality and accuracy of the final product. This article delves deep into the significance of die casting molds, the different types available, their manufacturing process, and the industries that benefit from them.
What is a Die Casting Mold?
A die casting mold is a tool used in the die casting process to shape molten metal into a specific form. It consists of two halves, known as the die, which, when closed, create a cavity into which the molten metal is injected. The precision of the mold is critical, as it directly influences the dimensions and surface finish of the casting. In essence, the die casting mold not only defines the shape but also determines the performance characteristics of the final metal product.
The Advantages of Using Die Casting Molds
Utilizing die casting molds offers numerous advantages that make this method a preferred choice in various industries:
- High Precision: Die casting allows for tight tolerances and intricate designs that would be challenging to achieve with other manufacturing processes.
- Durability: Cast products are typically very strong, making them ideal for industries requiring robust components.
- Cost-Effectiveness: Although the initial costs for manufacturing die casting molds can be high, the long-term benefits and reduced production costs justify the investment.
- Excellent Surface Finish: The smooth surfaces attained in die casting reduce the need for secondary machining processes, thereby saving time and resources.
- Complex Geometries: Die casting molds can produce parts with complex shapes that are difficult or impossible to achieve with other processes.
The Types of Die Casting Molds
There are primarily two types of die casting molds, each suited for different purposes:
1. Hot Chamber Die Casting Molds
Hot chamber die casting is typically used for metals with low melting points such as zinc, lead, and tin. In this process, the molten metal is kept in a reservoir that maintains a temperature conducive to casting. The major advantages include:
- Speed: Faster cycle times due to the quick operation of the injection system.
- Simplicity: Easier to set up and operate.
2. Cold Chamber Die Casting Molds
Cold chamber die casting is employed for metals with higher melting points, like aluminum and magnesium. In this methodology, the metal is melted in a separate furnace before being transported to the die. This process offers:
- Versatility: Suitable for a wider range of materials.
- Quality: The ability to produce high-quality aluminum die castings.
The Manufacturing Process of Die Casting Molds
The production of die casting molds involves several key steps:
1. Design and Engineering
The initial phase involves designing the mold based on the specifications of the final product. Advanced CAD software is often used to simulate the filling and cooling processes to ensure optimal performance.
2. Material Selection
The choice of materials is critical for mold longevity and performance. Common materials include:
- Steel: Offers high strength and resistance to wear.
- Aluminum: Lightweight and provides good thermal conductivity.
3. Machining
After the design is finalized, machining is conducted to create the mold cavities. This process involves milling, drilling, and grinding to achieve the desired shapes and tolerances.
4. Heat Treatment
Molds often undergo heat treatment to enhance their durability and resistance to wear. This step is essential for maintaining the structural integrity of the mold during the casting process.
5. Assembly and Testing
Once all components are crafted, the mold is assembled. Testing follows to ensure that it performs correctly under the intended operating conditions.
Applications of Die Casting Molds
Die casting molds serve a variety of industries, showcasing their versatility:
- Automotive: Production of engine components, transmission cases, and wheels.
- Aerospace: Manufacturing of lightweight and strong structural components.
- Electronics: Creating enclosures for devices, connectors, and other intricate parts.
- Consumer Goods: Producing household appliances, furniture hardware, and decorative items.
Advancements in Die Casting Mold Technology
The evolution of technology has brought significant improvements to die casting mold manufacturing, enhancing efficiency and quality. Innovations such as:
1. 3D Printing
3D printing technology is increasingly being used to create mold prototypes. This allows for rapid iteration and cost-effective adjustments in design before moving to production.
2. Simulation Software
Cutting-edge simulation tools help engineers predict how molten metal flows within the mold, allowing for modifications to minimize defects.
3. Advanced Materials
New materials, including high-performance alloys and coatings, increase mold durability and performance, reducing the frequency of replacements and maintenance.
Conclusion: The Future of Die Casting Molds
As the demand for precision, efficiency, and sustainable manufacturing practices grows, die casting molds will continue to play a pivotal role in metal fabrication. With ongoing advancements in technology and materials, the potential for innovation within this field is immense. Businesses looking to enhance their production capabilities and maintain a competitive edge would do well to invest in high-quality die casting molds and embrace the latest manufacturing processes.
In summary, understanding the importance of die casting molds is essential for manufacturers across various industries. It not only impacts the cost and quality of the products but also the overall efficiency of the manufacturing process. As companies seek to optimize their manufacturing operations, the role of skilled metal fabricators, like those at deepmould.net, becomes increasingly vital.